The Role of Fasteners and Machining in High-Quality Product Design
The Role of Fasteners and Machining in High-Quality Product Design
Blog Article
Navigating the World of Fasteners and Machining: Methods for Accuracy and Rate
In the complex realm of bolts and machining, the mission for accuracy and rate is a perpetual challenge that requires precise interest to information and strategic preparation. From understanding the diverse selection of bolt types to choosing optimum materials that can withstand strenuous needs, each step in the process plays an essential role in achieving the desired outcome.
Understanding Bolt Types
When choosing bolts for a task, recognizing the numerous kinds readily available is essential for making certain optimal efficiency and reliability. Bolts are available in a wide variety of kinds, each made for particular applications and demands. Screws are used with nuts to hold products with each other, while screws are versatile bolts that can be utilized with or without a nut, depending upon the application. Nuts, on the other hand, are inside threaded fasteners that companion with screws or bolts, providing a secure hold. Washers are essential for distributing the tons of the bolt and preventing damages to the product being secured. Furthermore, rivets are long-term fasteners that are optimal for applications where disassembly is not required. Recognizing the distinctions in between these bolt kinds is important for picking the right one for the task, ensuring that the connection is solid, resilient, and reliable. By choosing the ideal bolt type, you can maximize the performance and durability of your project - Fasteners and Machining.
Picking the Right Products
Comprehending the relevance of selecting the best products is extremely important in guaranteeing the ideal efficiency and integrity of the picked bolt kinds discussed previously. When it pertains to bolts and machining applications, the product option plays an essential function in determining the general stamina, longevity, deterioration resistance, and compatibility with the intended setting. Different materials provide varying homes that can dramatically influence the efficiency of the bolts.
Typical products utilized for bolts consist of steel, stainless steel, light weight aluminum, titanium, and brass, each having its distinct strengths and weak points. Steel is renowned for its high strength and sturdiness, making it suitable for a large range of applications. Choosing the right material entails thinking about variables such as toughness demands, ecological conditions, and budget plan restraints to guarantee the wanted performance and durability of the bolts.
Precision Machining Techniques
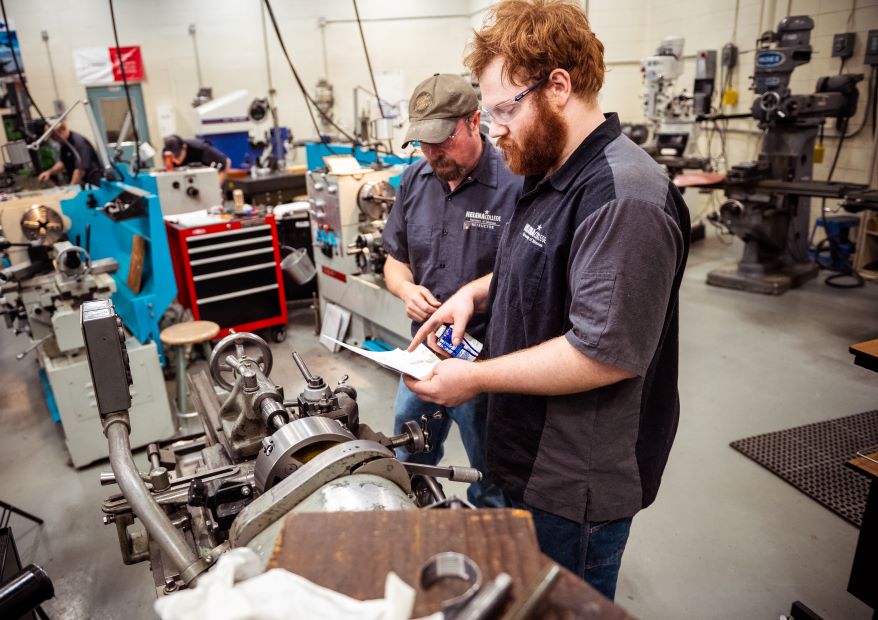
In enhancement to CNC machining, other accuracy methods like grinding, turning, milling, and boring play important roles in bolt production. Grinding assists achieve great surface area coatings and tight dimensional resistances, while turning is often made use of to create cylindrical parts with precise diameters. Milling and boring procedures are vital for forming and creating openings in bolts, ensuring they meet Website precise requirements and feature correctly.
Enhancing Speed and Effectiveness
To optimize fastener manufacturing procedures, it is important to improve procedures and carry out reliable strategies that complement precision machining methods. One vital technique for improving rate and performance is the execution of lean production concepts. By lowering waste and concentrating on continuous improvement, lean methods help optimize and eliminate bottlenecks workflow. Additionally, purchasing automation innovations can dramatically boost manufacturing rate. Automated systems can handle repetitive tasks with precision and rate, permitting employees to focus on even more facility and value-added tasks. Embracing Just-In-Time (JIT) stock management can also improve efficiency by making sure that the ideal products are offered at the best time, lessening excess stock and decreasing lead times. Promoting a culture of collaboration and interaction among team members can boost general efficiency by advertising transparency, problem-solving, and advancement. By combining these techniques, suppliers can attain a balance between speed and precision, ultimately improving their competitive side in the fastener market.
Quality Assurance Actions
Applying strenuous high why not try this out quality control steps is essential in guaranteeing the dependability and consistency of fastener items in the production process. Fasteners and Machining. Quality control measures incorporate different stages, starting from the option of raw materials to the last evaluation of the completed bolts. This includes assessing variables such as material durability, structure, and toughness to guarantee that the fasteners meet market criteria.
Regular calibration of devices and equipment is essential to preserve uniformity in production and make certain that fasteners satisfy the needed tolerances. Applying strict procedures for recognizing and addressing flaws or non-conformities is important in protecting against substandard products from going into the marketplace. view publisher site By developing a comprehensive quality assurance framework, producers can maintain the online reputation of their brand name and supply bolts that meet the greatest requirements of efficiency and durability.
Conclusion
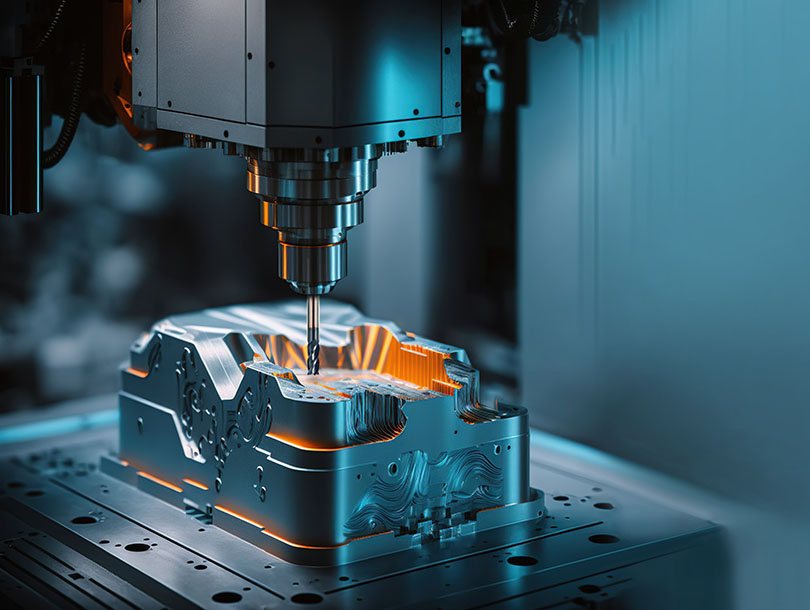
In the elaborate realm of fasteners and machining, the quest for accuracy and rate is a continuous obstacle that requires thorough focus to information and critical preparation. When it comes to bolts and machining applications, the product choice plays a critical duty in determining the total toughness, longevity, deterioration resistance, and compatibility with the desired atmosphere. Precision machining includes various advanced methods that guarantee the tight tolerances and specifications needed for bolts.In enhancement to CNC machining, various other accuracy methods like grinding, turning, milling, and exploration play crucial functions in fastener production.To maximize fastener production procedures, it is crucial to simplify procedures and execute efficient methods that match precision machining strategies.
Report this page